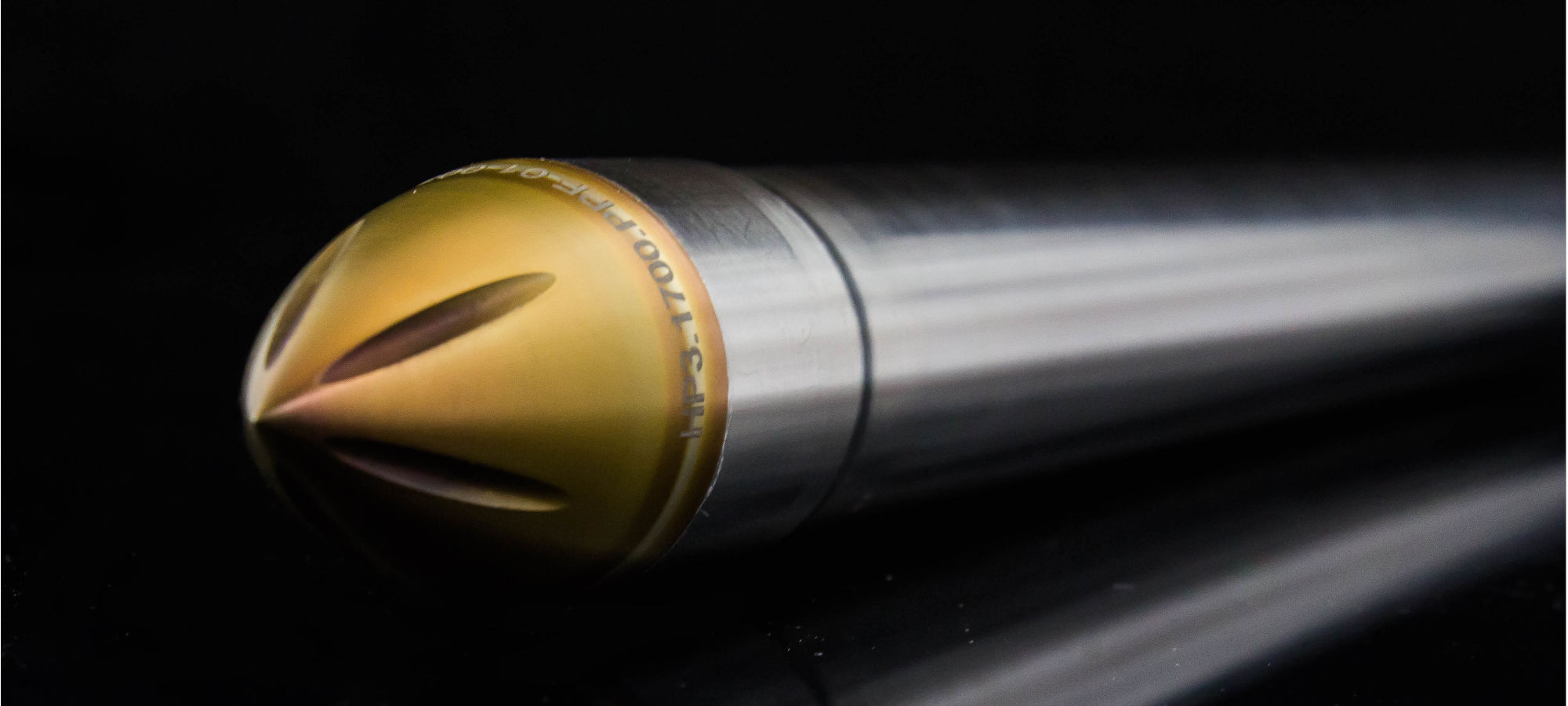
Astronika’s contribution involved mechanism design, optimization, performance and efficiency improvement, as well as further assembly and integration. Mechanical solutions and consultancy provided by Astronika were beneficial in the following fields:
- Limitation of power consumption and increase of system efficiency;
- Increase of stroke energy of the hammering mechanism and proper adjustment of the system resulting in the improvement of its progress per stroke and, hence, increased reliability (shorter work cycle needed to achieve a goal of five meters);
- Implementation of reliable relocking of the drive launch lock system;
- Load reduction of the system to lower the possibility of DC motor failure.
The instrument started its work in early 2019, and encountered multiple problems associated with the unexpected regolith parameters. Its full journey can be followed on DLR’s HP3 logbook. In January 2021, the instrument mission was discontinued. HP3 penetrometer was a pioneering mission, obtaining a ‘planetary first’ in the first self-propelled device to penetrate a planetary surface. The device developed the deepest man-made borehole on Mars, as of 2022.
Galago possesses a minimalistic design (up to 10 kg robotic platform), i.e. three symmetrical actuating legs distributed uniformly around its main platform, which allows the robot to vectorize its hopping in 3D space.
It is purposely designed for lunar gravity, which requires a highly energetic and efficient design of the actuator, its key sub-system. The actuator is compact and modular (110 x 190 x 82 mm and mass less than 1.5kg) and accumulates the energy (up to 50 J each) with low power consumption (below 5 W) by compressing drive springs in a rotary drum via a cam and a tether system pulled by a trolley on a ball screw. The actuator is then released by an electromagnet at a desired level of energy. The analyzed hopping efficiency is high (60-70%), which translates to 3-7 m of hopping height on the Moon depending on the surface type. As a result, Galago architecture can be scaled down to lower gravities and utilized in other missions for small moons (e.g. Phobos) or asteroids, which on the contrary is not possible the other way round for already known technologies for micro-gravity, e.g. MINERVA or MASCOT.

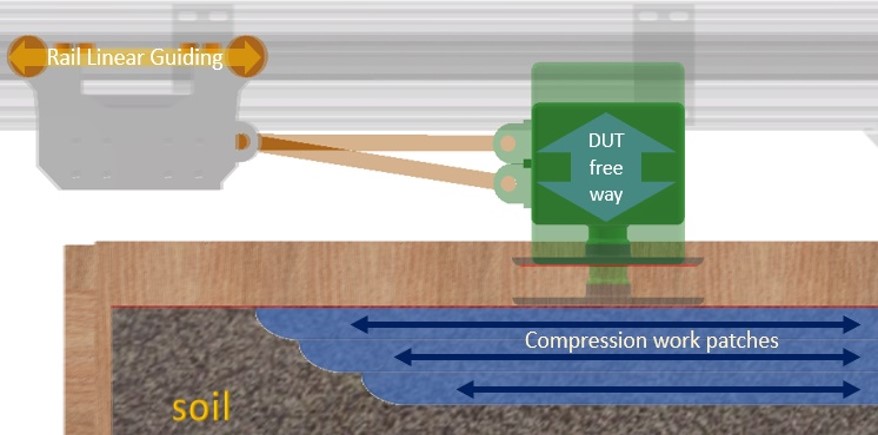
The project adapts terrestrial practices in site preparation and groundwork using baseplate compaction. The device can be mounted as a front or backload of a rover, or directly under the rover, thus allowing for large-scale mobility. The main application of regolith compaction is to provide a preliminary horizontal construction capability in building landing-launch pads for heavy landers. No terrestrially-sourced binders are needed in the process. Consecutive sintering/melting and compaction can however be beneficial for further geotechnical reinforcement.
The project targets TRL 4 subject to a test campaign in a 1.5-tonne regolith sandbox. At the current stage, the device fits within a 30x30x30 cm envelope, with a mass of 30 kg, most of which is used by the actuator. Large energies and reaction forces are necessary to fulfil the regolith compaction tasks, that is why it is beneficial for the device to be lightweight on launch, and filled will rocks and regolith after landing.
Apart from construction, the device can be used as an active source of seismic waves, acting similarly to vibrator trucks on Earth used in seismic prospecting.